Why Your Powder Coating Oven’s Cool-Down Zone Deserves More Credit
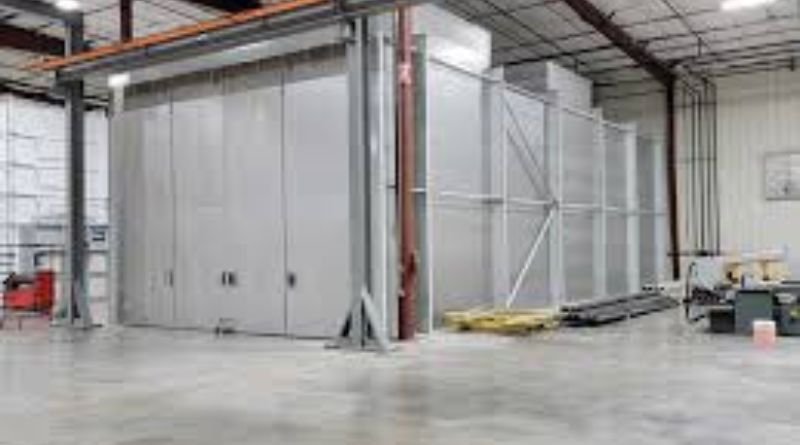
When it comes to powder coating ovens, most of the attention tends to focus on the heating process. While the heating zone is important for curing the coating, the cool-down zone deserves just as much recognition. This often overlooked part of the oven plays a key role in ensuring the quality, durability, and overall performance of the coated product. Let’s explore why giving more attention to the cool-down zone can make a big difference in the final outcome of your powder coating process.
Preventing Surface Defects with Controlled Temperature Descent
One of the most significant benefits of a well-designed cool-down zone is its ability to prevent surface defects on the coated material. When a powder coating oven cools down too quickly, it can lead to issues like bubbling, cracking, or other imperfections in the finish. These defects occur because the sudden change in temperature can cause the material to shrink or expand unevenly, leading to stress on the coating layer.
By allowing for a controlled temperature descent in the cool-down zone, powder coating ovens help ensure that the material cools at a steady rate. This gradual cooling process reduces the likelihood of defects and ensures a smoother, more uniform finish. In industries where appearance and surface quality are essential, such as automotive or furniture manufacturing, this step can’t be ignored.
Stabilizing Coated Layers for Enhanced Durability
Durability is another key factor when it comes to powder coating, especially in applications where the coated product is exposed to harsh conditions. The cool-down zone in a powder coating oven is essential for stabilizing the coating layers, ensuring they bond securely to the underlying material.
When the temperature is reduced gradually, the coated layers have time to solidify properly, forming a more durable and resistant surface. If the cooling process happens too quickly, the layers may not have enough time to stabilize, resulting in a less durable finish. Over time, this can lead to chipping, peeling, or premature wear of the coating, compromising the product’s lifespan.
Minimizing Thermal Shock to Maintain Structural Integrity
One of the hidden challenges in powder coating is the risk of thermal shock, especially when dealing with metals or materials that are sensitive to rapid temperature changes. When an object comes out of the high heat of a powder coating oven, a quick temperature drop can cause sudden expansion or contraction, leading to cracks or warping in the material itself.
The cool-down zone works to minimize thermal shock by controlling the rate at which the object cools down. This controlled cooling helps the material adjust gradually, reducing the stress on both the coating and the substrate. By maintaining structural integrity, the cool-down zone ensures that the coated product remains free from distortion and maintains its original shape and strength.
Ensuring Uniform Finish by Slowing Down Cooling Rates
Achieving a consistent, uniform finish is one of the main goals in powder coating, and the cool-down zone is key to making this happen. When the cooling process is rushed, different areas of the coated object may cool at different rates, leading to uneven curing and an inconsistent finish.
By slowing down the cooling rate, powder coating ovens ensure that the entire surface cools at the same pace. This uniform cooling allows the coating to settle evenly, preventing color variations, texture inconsistencies, or rough patches. The result is a smooth, polished finish that looks professional and meets the high standards of industries like electronics, appliances, or decorative items.
Preserving Adhesion Strength Through Gradual Heat Dissipation
Adhesion strength is what keeps the coating firmly attached to the surface, and the cool-down zone plays a pivotal role in preserving this bond. When a coating is exposed to a sudden temperature drop, the bond between the coating and the substrate can weaken, leading to adhesion failure over time.
In powder coating ovens, the gradual dissipation of heat during the cool-down phase allows the coating to bond more securely with the surface material. This enhanced adhesion strength ensures that the coating remains intact, even under tough conditions like abrasion, chemical exposure, or high wear environments.
Reducing Internal Stress in Complex Geometries for Long-Term Performance
In global industries where products come in all shapes and sizes, complex geometries are common. Whether it’s a finely detailed metal part or a large piece with intricate designs, these items can be more prone to internal stress during the powder coating process. Rapid cooling can exacerbate these stresses, leading to cracks, distortions, or even breakage.
By utilizing the cool-down zone effectively, powder coating ovens reduce internal stress within these complex geometries. The slow, steady cooling process gives the material time to adapt, releasing any built-up tension that might otherwise compromise its long-term performance. For products that require precision and durability, like medical devices or specialized equipment, this careful management of internal stress is vital.